Aerospace
Aerospace
CAD/CAE/CFD technologies are integral to the modern aerospace industry, enabling engineers to design, analyze, and optimize aircraft and spacecraft with unprecedented precision and efficiency. The integration of CAD/CAE/CFD technologies is crucial for the aerospace industry to maintain its competitive edge and continue pushing the boundaries of flight and space exploration.
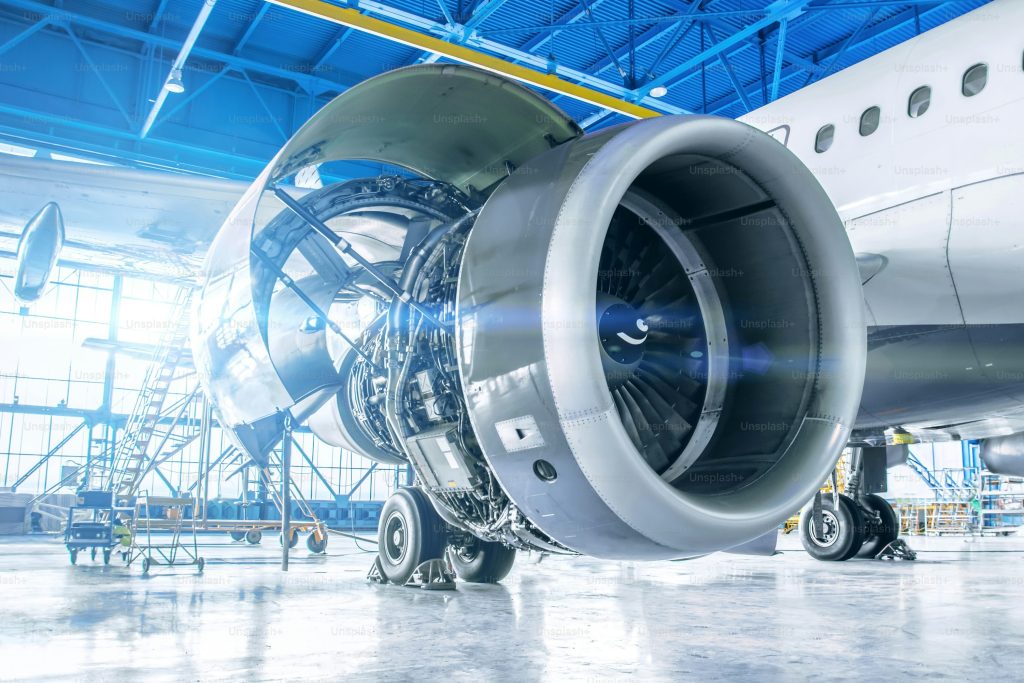
Significance of CAD/CAE/CFD in Aerospace:
- Reduced Development Time and Costs: Virtual prototyping and simulation significantly
cut down on the need for expensive physical prototypes and testing. - Enhanced Performance and Safety: These tools enable rigorous analysis of aerodynamic
performance, structural integrity, and thermal behavior, leading to safer and more
efficient designs. - Design Optimization: CAD/CAE/CFD facilitate the exploration of numerous design
iterations and the optimization of complex geometries. - Compliance with Stringent Regulations: Aerospace products must meet rigorous safety
and performance standards, and these technologies help ensure compliance.
CADELL technologies offer a wide range of services to the aerospace industry: –
- Aircraft Design:
Creating detailed 3D models of airframes, wings, propulsion systems, and other components.
Designing complex aerodynamic surfaces for optimal performance.
Developing detailed manufacturing drawings and assembly instructions.
Finite Element Analysis (FEA):
- Analyzing structural integrity under various loads (e.g., flight loads, landing loads, pressure loads).
- Performing modal analysis to determine natural frequencies and vibration modes.
- Analyzing fatigue life and damage tolerance.
- Performing crash simulations for aircraft safety.
Thermal Analysis:
- Simulating heat transfer in engine components, avionics systems, and thermal protection systems.
- Analyzing thermal stresses and deformations.
Computational Structural Dynamics (CSD):
- Analyzing the interaction between fluid flow and structural deformation.
- Analyzing aeroelasticity.
Composite Material Analysis:
- Simulating the behavior of advanced composite materials used in aerospace structures.
Aerodynamic Analysis:
- Simulating airflow around aircraft and spacecraft to optimize lift, drag, and stability.
- Analyzing supersonic and hypersonic flows.
- Analyzing the performance of air intakes and exhaust systems.
Propulsion System Analysis:
- Simulating combustion processes in jet engines and rocket engines.
- Analyzing the performance of turbomachinery.
- Analyzing the flow within rocket nozzles.
Heat Transfer Analysis:
- Simulating heat transfer in engine cooling systems and thermal protectionsystems.
How the Aerospace Industry would be Benefited:
- Improved Aerodynamic Performance: Optimizing aircraft and spacecraft designs for increased efficiency and performance.
- Enhanced Structural Integrity: Ensuring the safety and reliability of aerospace structures.
- Reduced Development Costs: Minimizing the need for physical prototypes and testing.
- Faster Time to Market: Accelerating the design and development process.
- Increased Innovation: Facilitating the exploration of new design concepts and technologies.